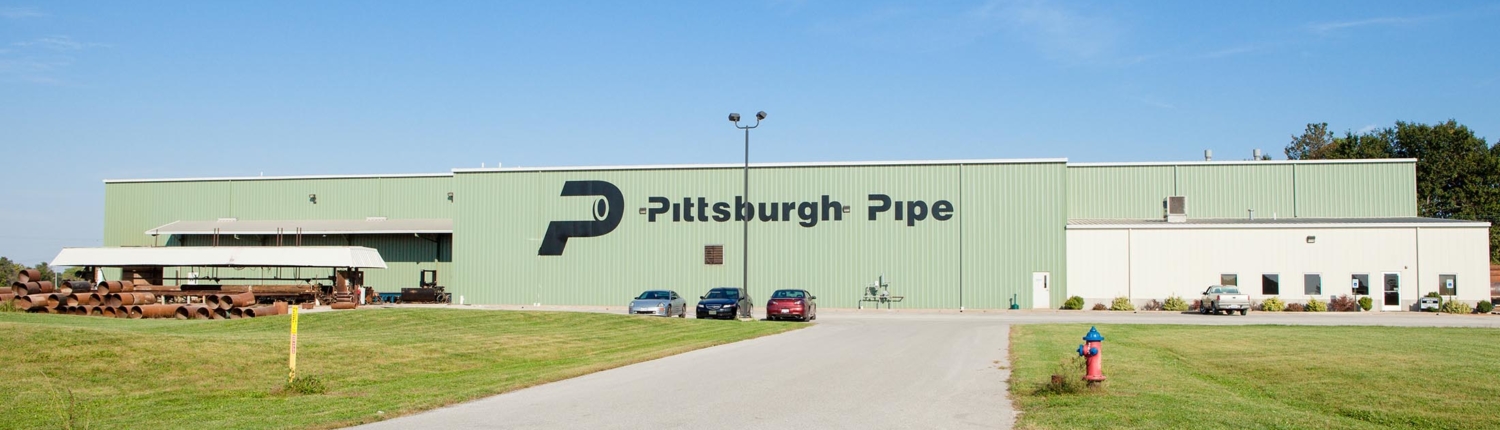
When you have a pair of autonomous robots that are designed to crawl through miles of steel pipes at the US Department of Energy’s former uranium enrichment plant with a mission to identify dangerous uranium deposits on pipe walls, and you need specially designed steel casing pipe fabricated to test them, who do you turn to?
Pittsburgh Pipe.
The Job Requirements:
When a task is too dangerous for a human, send in a robot. Carnegie Mellon University developed two uranium-sniffing robots to search through pipes at the Department of Energy’s former enrichment plant in Piketon, Ohio. Uranium levels in these pipes were more accurately measured internally rather than externally, in addition to saving the labor costs of finding someone with the fortitude to crawl through radiated pipes and the cost of the safety equipment needed to safely complete the job.
The issue… before these robots could start their mission, they needed to be tested. That’s where the expertise of Pittsburgh Pipe came in.
Pittsburgh Pipe – The Perfect Partner:
It all started with a Google search for “Steel Casing Pipe”. Red Whittaker, the director of the CMU Field Robotics Center, was looking for a pipe fabrication company that had experience in customization, pipe fabrication, and an open mind. After Googling “Steel Casing Pipe” he came across Pittsburgh Pipe and learned that this was a company that specialized in steel casing pipe, fabrication, and special coatings. After a call to Sales Rep Danny Honkamp, Pittsburgh Pipe got to work designing the pipe Red needed to test his robots.
Producing Results with Advanced Fabrication:
Red needed two 10 foot sections of pipe; one 40” inside diameter x .375” wall, and the other 30” inside diameter x .375” wall. Both pipes needed extensive fabrication to allow for various test samples to be attached and removed from the pipes.
Each pipe contained eighteen (18) 9” x 12” pre-cut removable ports to be used for collecting data from the autonomous robots during testing. Pittsburgh Pipe zipper cut these ports for the Professor on our Koike CNC (computer numerical control) Burn Table, while the steel plate was still in the flat sheet form (before rolling), in the precise locations needed pursuant to the Professor’s detailed drawings.
This was an exciting project for Danny and the Pittsburgh Pipe team as it gave us an opportunity to prove our dedication to precise craftsmanship, our advanced fabrication capabilities, and our ability to solve issues for our customers.
The Pittsburgh Pipe Advantage
Projects like this underscore our commitment to finding the right solution for our customers, not overthinking the issue, not trying to cram customer’s needs into predetermined categories. Using our knowledge and experience to solve the issue, we leave our customers with a solution they can not simply live with, but that solves each and every one of their problems and requirements.
Contact Us at 2331 Hampton Ave., St. Louis, MO 63129 or click to call us!
About Pittsburgh Pipe
At Pittsburgh Pipe, we offer many different products and services. We strive to be the best at what we do and to provide the best products. We put a lot of time and effort into making sure our steel pipe is the best in the industry.
Serving Coast to Coast
HEADQUARTERS
2331 Hampton Avenue
Saint Louis, MO 63139
PHONE
314.383.5300
800.325.2653